Why Building Your Own Wall Cabinets is the Smarter Choice
Buying pre-made wall cabinets for your kitchen, garage, or home office can put a serious dent in your budget. Prices for quality wall cabinets often range from $150 to $500 per unit, and custom options can easily soar past $1,000. While pre-assembled cabinets offer convenience, they can lack the durability, customization, and satisfaction of a well-crafted DIY project. Plus, pre-made options can still leave you compromising on design or dimensions that don’t quite fit your space.
The Problem: High Costs and Limited Flexibility
Store-bought wall cabinets are often expensive and restrict you to standard designs. If your space has unique dimensions, you’re out of luck unless you opt for high-end custom solutions, which come with hefty price tags. For many homeowners, especially DIY enthusiasts, this makes off-the-shelf cabinets frustratingly limiting. Whether for a kitchen, garage, or workspace, having complete control over the design is key to achieving a perfect fit.
The Solution: DIY Wall Cabinets
With a DIY plan, you unlock the ability to create cabinets tailored to your exact needs, saving you from inflated costs while ensuring a perfect match for your space. By building your own, you have the flexibility to:
- Customize dimensions, materials, and finishes.
- Maximize vertical storage space efficiently.
- Add features like adjustable shelves and soft-close hinges without the cost of upgrades.
And the best part? You’ll develop woodworking skills along the way, making future projects even easier and more rewarding.
Cost Efficiency:
Investing in some basic tools is a small price to pay compared to the cost of store-bought cabinets. Once you own the tools, they can serve you across many projects, not just this one. Materials like 3/4″ and 1/4″ plywood for wall cabinets cost far less than pre-made units, ensuring your budget stretches further. The best part? You’re putting your money into quality materials, not brand markups.
DIY Wall Cabinet Features That Save You More
- Durable Materials: 3/4″ plywood construction ensures long-lasting strength, far superior to particleboard options sold in many stores.
- Perfect Fit: Tailor your cabinet’s width, height, and depth to fit your space without compromises.
- Personalized Finish: Choose the paint, stain, or veneer that complements your home’s aesthetic—without upgrade fees.
- Skill Development: With each cut and assembly step, you gain practical skills and the satisfaction of building something from scratch.
Why This DIY Plan Solves the Problem
This plan takes the complexity out of building your own wall cabinets by breaking the project down step by step. You don’t need to be a professional woodworker to achieve professional results. The plan provides:
- Clear instructions with every step laid out.
- Visual diagrams for easy-to-follow guidance.
- Lumber and tool shopping lists so you get everything you need upfront.
- Cut optimization tips to minimize material waste.
- Budget estimates so you can plan your costs accurately.
What’s Included in the DIY Wall Cabinet Plan
- Step-by-Step Instructions: Clear, easy-to-follow written instructions that guide you from the first cut to the final installation.
- Detailed Diagrams: Visuals that highlight the exact placement of each piece and fastener, ensuring the assembly is straightforward.
- Tools List: A checklist of the tools you’ll need, with suggestions for affordable options if you’re starting your collection.
- Lumber and Materials Lists: Precise measurements and quantities to make shopping simple and efficient.
- Cut Optimization Guide: A layout that shows how to get the most from each sheet of plywood, reducing waste and saving money.
- Budget Overview: Estimated costs so you can keep your project on track, with tips for sourcing affordable materials.
- Print-Friendly Format: Take the plans directly to your workshop for easy reference as you build.
- Beginner-Friendly Design: Even if you’re new to woodworking, you can follow along confidently. Every step is designed to be accessible.
Ready to Build?
With this DIY wall cabinet plan, you’ll save money, sharpen your skills, and gain complete control over your storage solutions. There’s no need to settle for pre-made cabinets that don’t quite fit your needs. This project ensures you get exactly what you want—whether it’s for the kitchen, garage, or a home office—all while keeping your budget in check.
Time
(varies with experience)
Cost
$100-$180 per wall cabinet (Costs may vary based on location and supplier.)
Skill level required
Beginner
DIY Wall Cabinet PDF Plan
What is included in the PDF download?
- Easy to read step by step instructions
- Material list
- Tools needed
- Helpful links to materials and tools needed
Tools and Materials Needed for Wall Cabinet Construction
Available wit the purchase of the DIY plan PDF.
Lumber Shopping & Cut List
Available wit the purchase of the DIY plan PDF.
Common Wood Types for Cabinets
1. Plywood
Overview: Plywood is an engineered wood made from thin layers of wood veneer glued together. It’s a top choice for cabinet construction due to its strength and versatility.
Pros:
- Strength and Stability: Ideal for structural components like sides, backs, and bases.
- Cost-Effective: Provides strong support without the high cost of solid wood.
- Variety of Grades: Available in grades from A to C, with A-grade offering a smooth finish suitable for visible areas.
- Availability: Widely available at Home Depot and Lowe’s in various thicknesses (1/4″, 1/2″, 3/4″) and types, including hardwood veneers like oak, maple, and birch.
Cons:
- Edge Finishing: Requires additional finishing, like edge banding, for exposed edges.
- Moisture Sensitivity: Can warp if not properly sealed against moisture.
Recommendation: Use 3/4″ plywood for cabinet carcasses and shelves as detailed in the DIY plan for durability and strength.
2. MDF (Medium-Density Fiberboard)
Overview: MDF is made from wood fibers bonded with resin under pressure, offering a smooth surface perfect for painting.
Pros:
- Smooth Surface: Great for painted finishes due to its uniform surface.
- Affordable: Less expensive than plywood and solid wood.
- Uniformity: No grain or knots, making it easier to work with for detailed cuts.
Cons:
- Poor Moisture Resistance: Swells and deteriorates when exposed to moisture.
- Heavy: Its density makes it heavier and more challenging to handle.
Recommendation: Use MDF for cabinet doors and decorative panels, but avoid in moisture-prone areas unless sealed.
3. Solid Wood Options
Solid wood adds a classic, high-quality look to cabinets and is typically used for doors, drawer fronts, and face frames.
Maple:
- Pros: Hard and durable, smooth grain for staining or painting.
- Cons: Moderate cost, can be more expensive than birch.
- Best For: High-traffic areas needing durability.
Oak:
- Pros: Strong and wear-resistant with a traditional grain.
- Cons: Heavy grain can be difficult to paint smoothly.
- Best For: Traditional or rustic cabinet styles.
Cherry:
- Pros: Elegant with a rich patina that deepens over time, smooth grain.
- Cons: Higher cost, softer than maple, prone to dents.
- Best For: High-end, refined cabinet designs.
Birch:
- Pros: Economical, easy to work with, takes stain well.
- Cons: Softer than other hardwoods, more susceptible to scratches.
- Best For: Budget-friendly projects that still want a hardwood look.
Availability: Home Depot and Lowe’s often stock these woods in various formats, including solid lumber and veneer plywood.
Woods to Avoid for Cabinets
Pine:
- Cons: Soft and prone to damage, knots can bleed through finishes.
- Best For: Only recommended for rustic or decorative uses.
Particleboard:
- Cons: Weak, prone to sagging and moisture damage, not durable.
- Best For: Avoid for structural components; limited to low-cost interiors.
Industry Standards for Cabinet Wood in the USA
- Plywood: The go-to for structural integrity in cabinet bases, sides, and shelving.
- MDF: Preferred for painted finishes, especially on doors and panels.
- Solid Wood: Typically used for face frames, doors, and drawer fronts where aesthetics and durability are key.
Where to Buy
For DIY builders, the most convenient sources are major retailers like Home Depot and Lowe’s, which carry a variety of plywood, MDF, and solid wood suitable for cabinet projects. Always check availability and compare grades to ensure you’re getting the best material for your specific needs.
Final Tips
- Check Wood Grades: For plywood, choose higher grades for visible areas.
- Plan for Moisture: Use moisture-resistant wood or seal properly in high-humidity areas like kitchens and bathrooms.
- Evaluate Costs: Balance your budget with the quality needed for your project; sometimes spending a bit more on higher-quality wood can save costs in the long run through durability.
Choosing the right wood is a critical step in building cabinets that are both beautiful and functional. This guide ensures you’re equipped with the knowledge to make the best decision for your DIY cabinet project, aligning with the industry standards and what’s readily available at popular home improvement stores.
Step 1: Prepare the Wall Cabinet Side Panels
In this step, you will modify two side panels by cutting grooves for dado joints and the back panel, and drilling shelf pin holes. This will prepare the panels for the assembly process.
Follow these steps carefully to ensure the panels are correctly prepared.
1.1 Gather Materials and Tools
- Materials:
- Two 3/4″ thick plywood sheets, each measuring 12″ x 42″.
- Tools:
- 23/32″ straight router bit
- 1/4″ straight router bit
- 1/4″ drill bit
- Shelf pin jig
- Router
- Drill
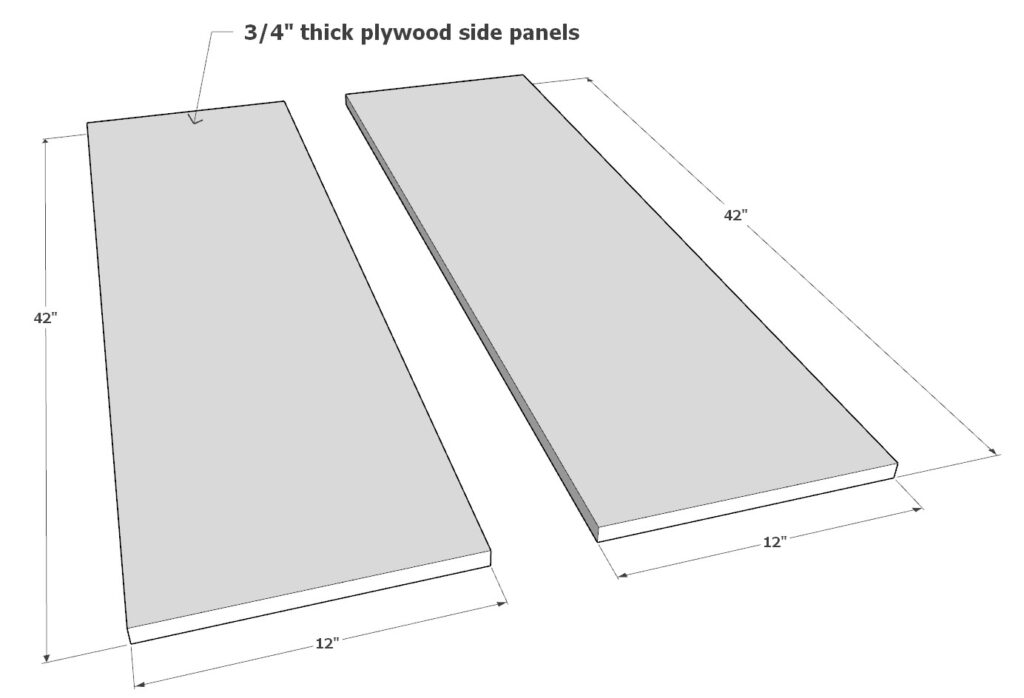
1.2 Cut Dado Grooves for the Floor and Ceiling Panels
- Set up your router with the 23/32″ straight router bit.
- Set the router depth to cut a 1/4″ deep groove.
- Mark the locations for the grooves:
- One groove near the bottom edge (for the floor panel).
- One groove near the top edge (for the ceiling panel).
- Cut the grooves on both side panels in the same locations using the 23/32″ bit.
- These grooves will act as dado joints where the floor and ceiling panels will attach.
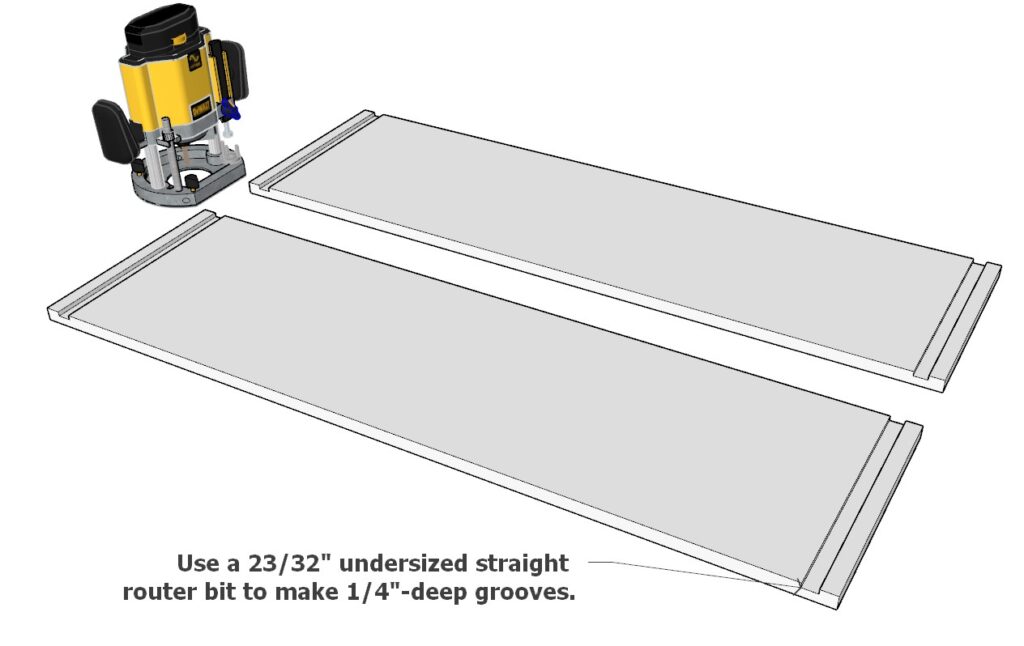
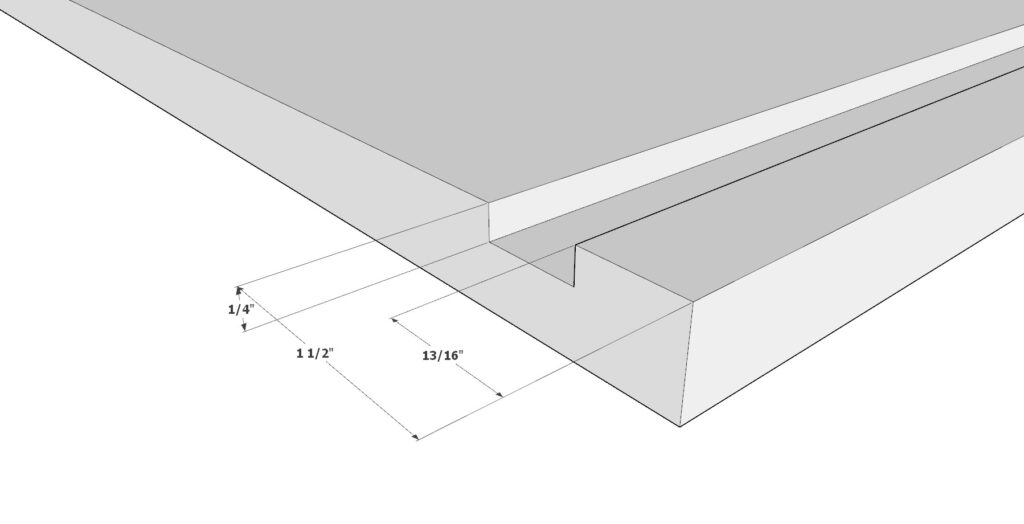
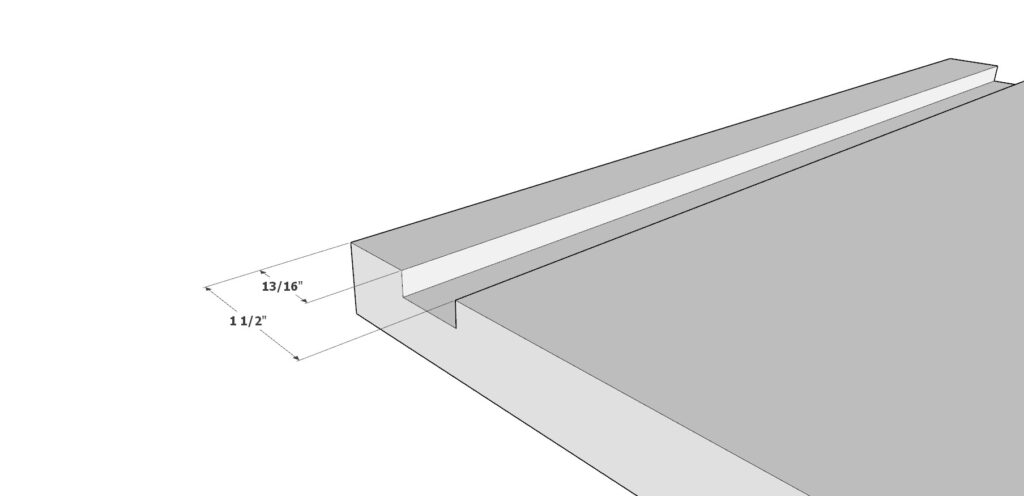
1.3 Cut the Groove for the Back Panel
- Switch to the 1/4″ straight router bit on your router.
- Set the depth to 1/4″.
- Cut an additional groove along the back edge of both side panels.
- This groove will hold the back panel securely in place.
- Ensure the grooves are clean and free of debris for a snug fit during assembly.
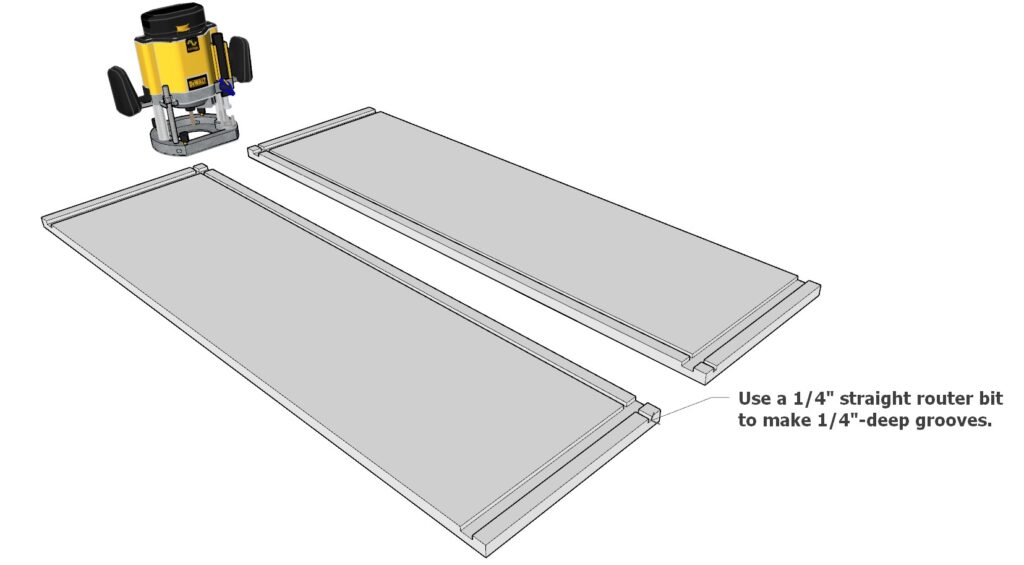
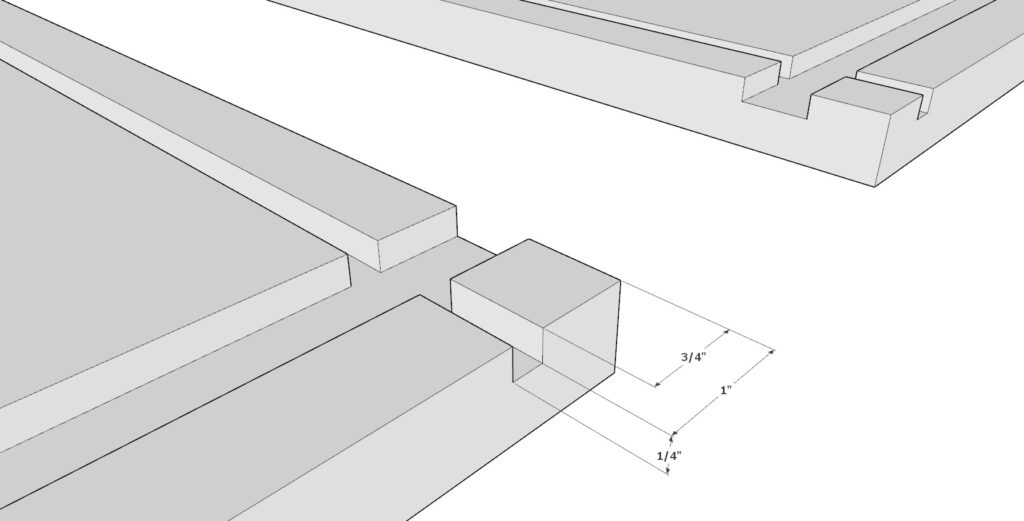
1.4 Drill Shelf Pin Holes
- Use the shelf pin jig to help with accurate hole spacing.
- Mark the drilling locations for shelf pin holes on the interior sides of both panels.
- Attach the 1/4″ drill bit to your drill.
- Drill evenly spaced holes along the marked lines, following the jig for consistency.
- Must be 2 inches (25 to 50 mm) from the front and back edges of the cabinet.
- These holes will allow you to use adjustable shelf pins for the cabinet.
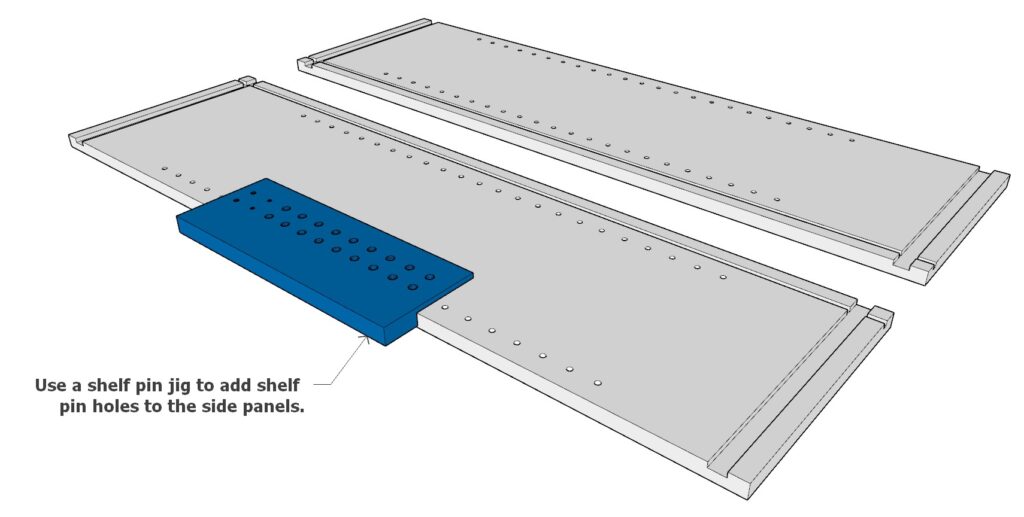
1.5 Verify the Panels
By the end of this step, you should have two mirror-image side panels. Each panel should have:
- 23/32″ grooves at the top and bottom for the floor and ceiling panels.
- 1/4″ grooves along the back edge for the back panel.
- Shelf pin holes drilled neatly and evenly using the jig.
Final Check:
- Ensure all cuts are clean and consistent.
- Double-check that both side panels mirror each other exactly—any misalignment can cause issues during assembly.
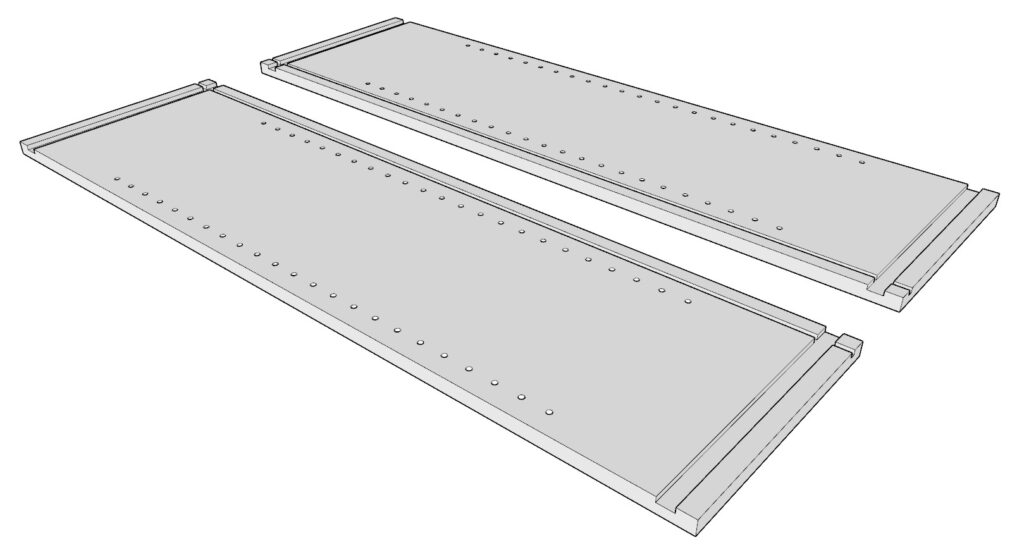
Step 2: Prepare the Ceiling, Floor, and Back Panels
In this step, you will modify the ceiling and floor panels to fit with the back panel, ensuring everything is ready for assembly. You will also introduce the back panel itself, so all these components are prepared for integration in the next step.
2.1 Gather Materials and Tools
- Materials:
- Two 3/4″ thick plywood sheets, each measuring 12″ x 31″ (ceiling and floor panels).
- One 1/4″ thick plywood sheet, measuring 39-1/2″ x 31″ (back panel).
- Tools:
- 1/4″ straight router bit
- Router

2.2 Cut the Groove for the Back Panel
- Attach the 1/4″ straight router bit to your router.
- Set the depth to 1/4″ to match the thickness of the back panel.
- Mark the location of the groove on the rear side of both the ceiling and floor panels.
- This groove will run along the back edge of both panels.
- Carefully cut the groove along the back edge of both panels, ensuring it aligns properly.
- This groove will later accommodate the back panel to ensure a flush fit.
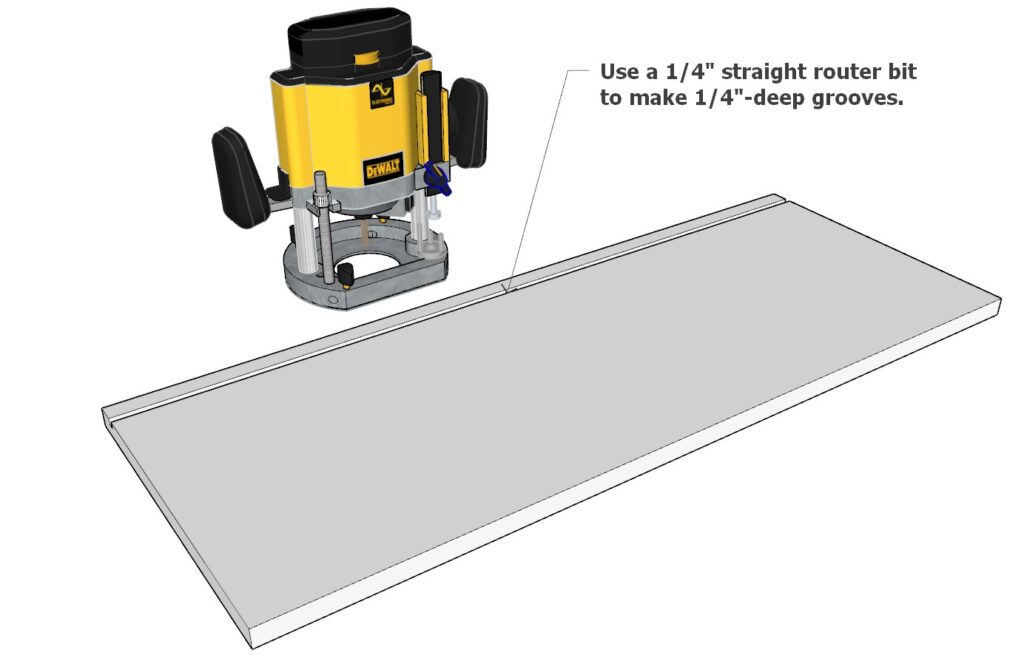
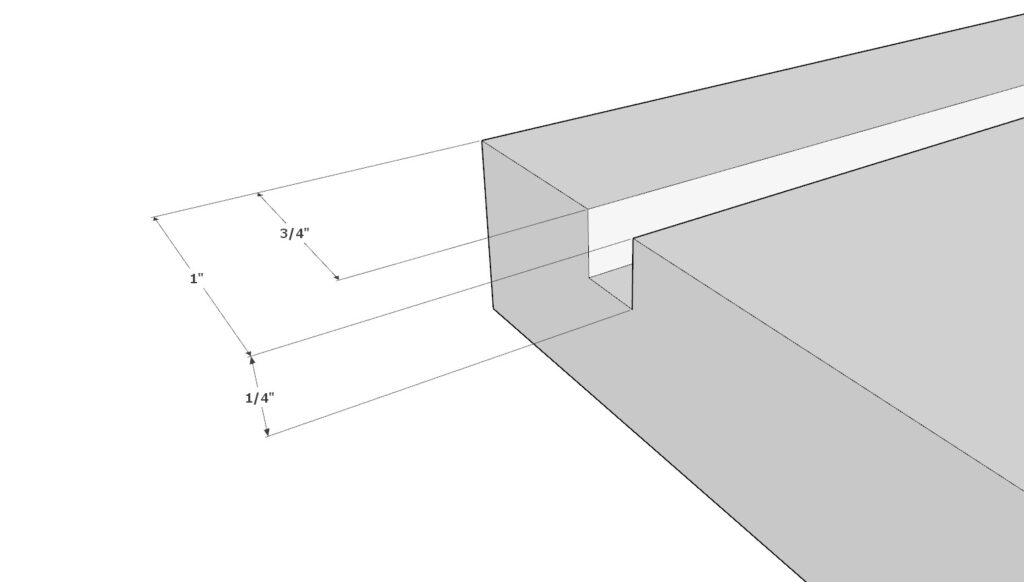

2.3 Prepare the Back Panel
- Take the 1/4″ thick plywood sheet measuring 39-1/2″ x 31″.
- Check that the back panel fits smoothly into the grooves you just cut on the ceiling and floor panels.
- Set the back panel aside with the ceiling and floor panels to have all components ready for the next step.
2.4 Verify the Components
By the end of this step, you should have:
- Two 3/4″ plywood panels (ceiling and floor) with 1/4″ grooves cut along the back edges.
- One 1/4″ thick back panel (39-1/2″ x 31″) ready for integration.
- All components neatly prepared and aligned for the upcoming assembly.
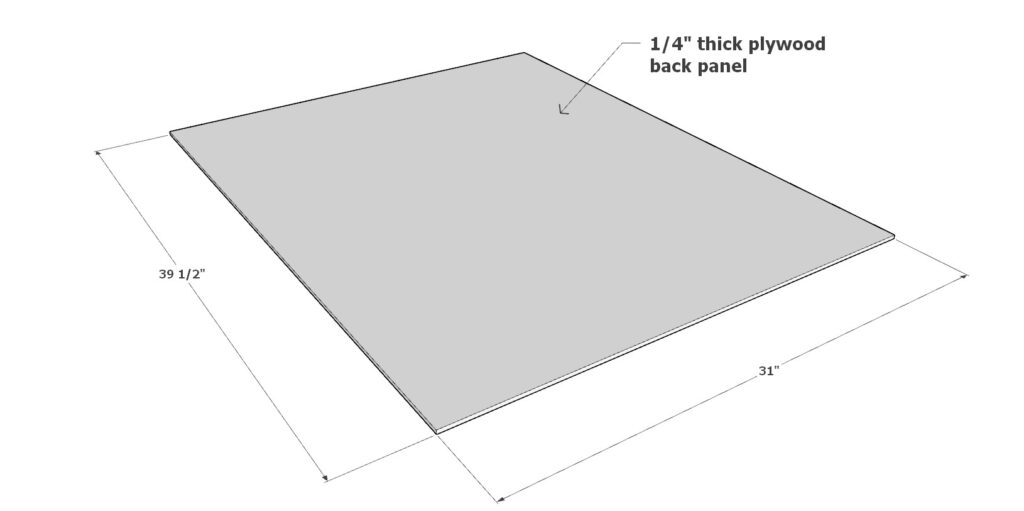
Step 3: Assemble the Cabinet Carcass
In this step, you will integrate the side panels, ceiling and floor panels, and the back panel to build the main structure, or carcass, of your wall cabinet.
3.1 Gather Materials and Tools
- Materials:
- Two side panels from Step 1
- One ceiling panel and one floor panel from Step 2
- One back panel from Step 2
- Wood glue
- Tools:
- Clamps (wood clamps)
- Sandpaper (fine-grit)
3.2 Attach the First Side Panel
- Take one of the side panels from Step 1.
- Apply wood glue along the dado joint (23/32″ groove) where the ceiling and floor panels will fit.
- Insert the floor panel and ceiling panel into the corresponding grooves on the side panel.
- Pro Tip: If the panels feel tight, use fine-grit sandpaper to lightly sand the edges. This will ensure a smooth fit, but be careful not to over-sand.
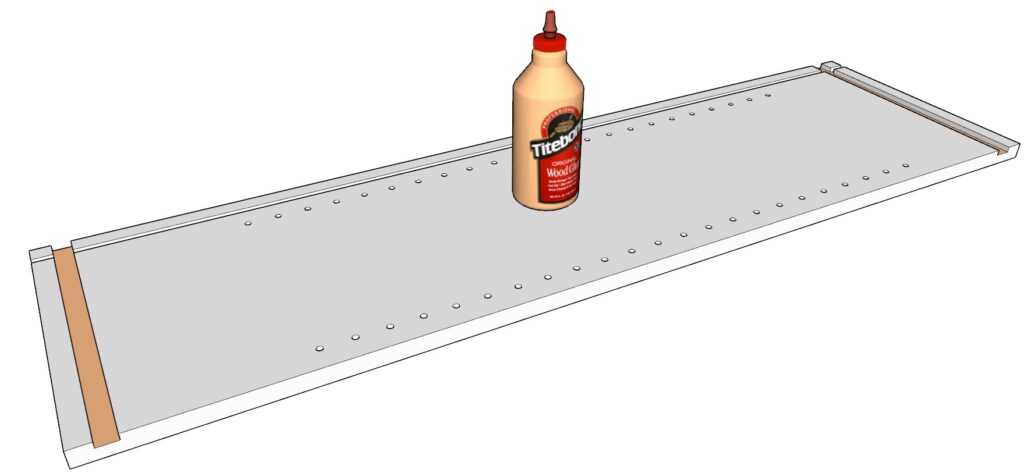
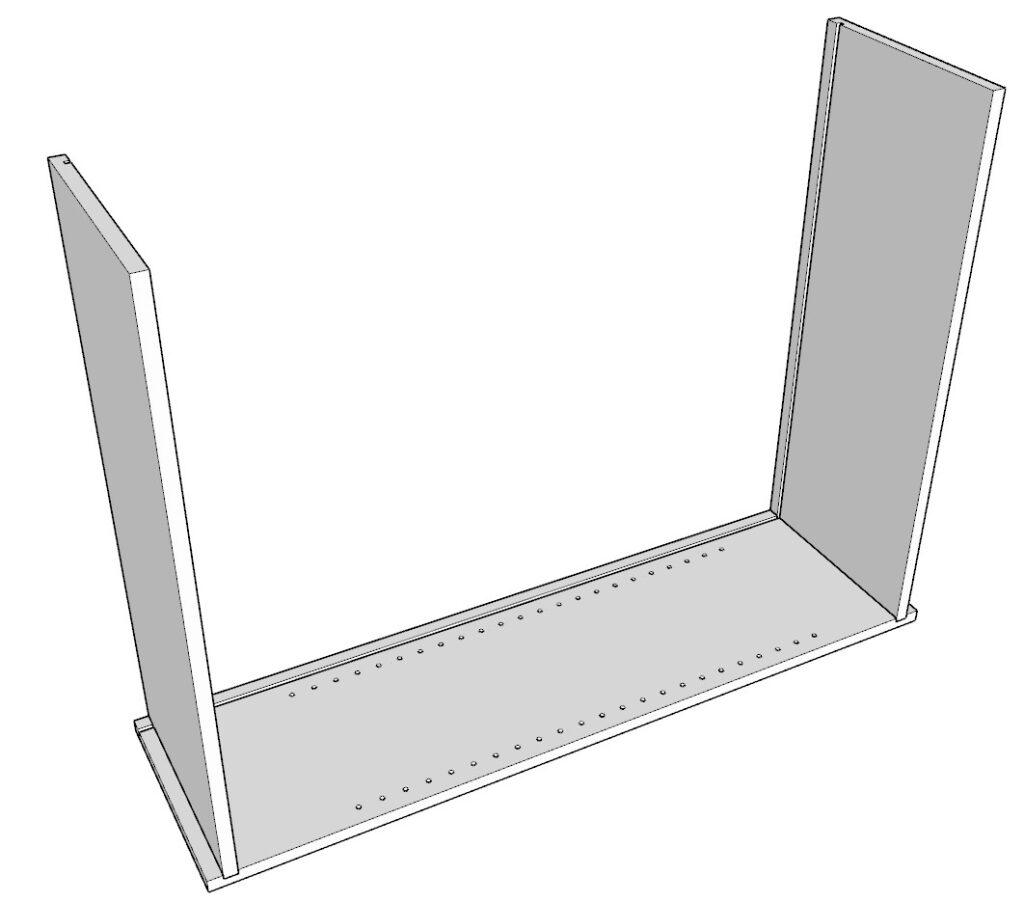
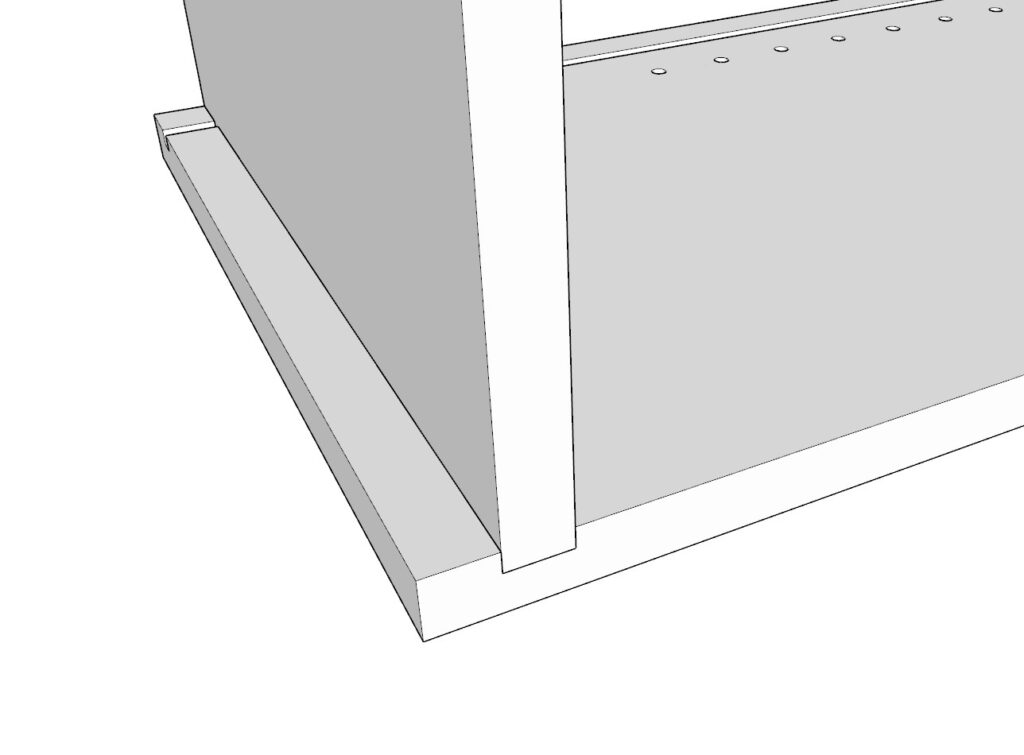
3.3 Insert the Back Panel
- Slide the back panel (from Step 2) into the 1/4″ grooves along the rear edges of the ceiling, floor, and side panels.
- Ensure the back panel is flush and fits snugly into the grooves.
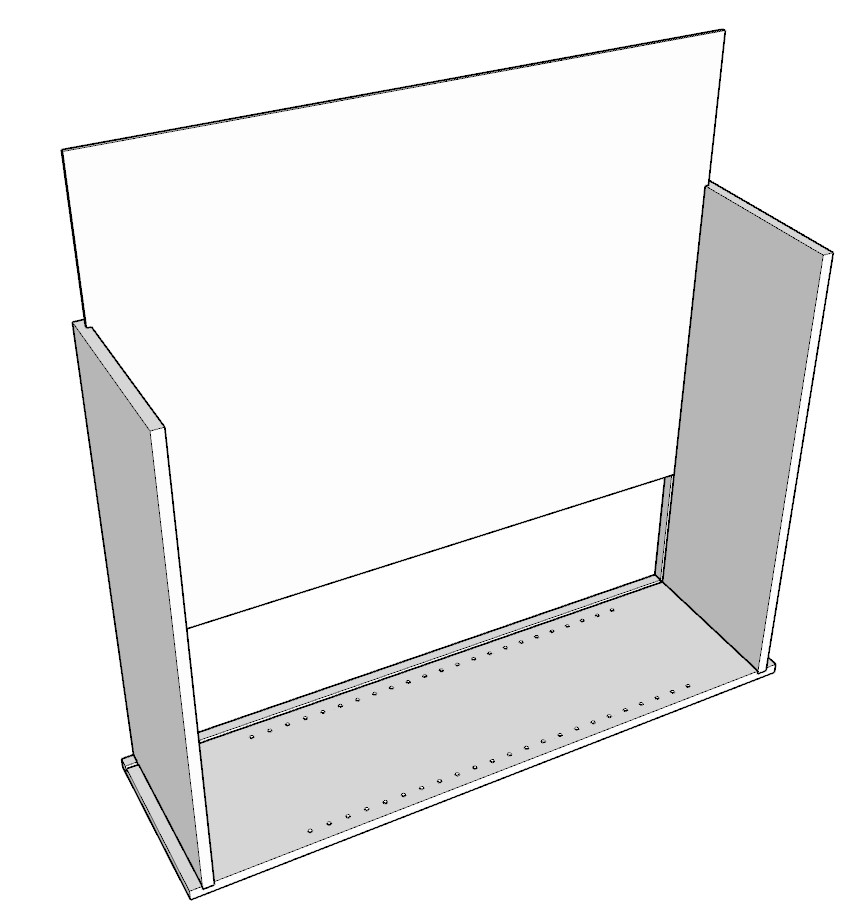
3.4 Attach the Second Side Panel
- Apply glue along the dado joint of the second side panel.
- Align the second side panel with the ceiling and floor panels, ensuring the grooves line up properly.
- Gently slide the second side panel into place, making sure all panels fit neatly together.
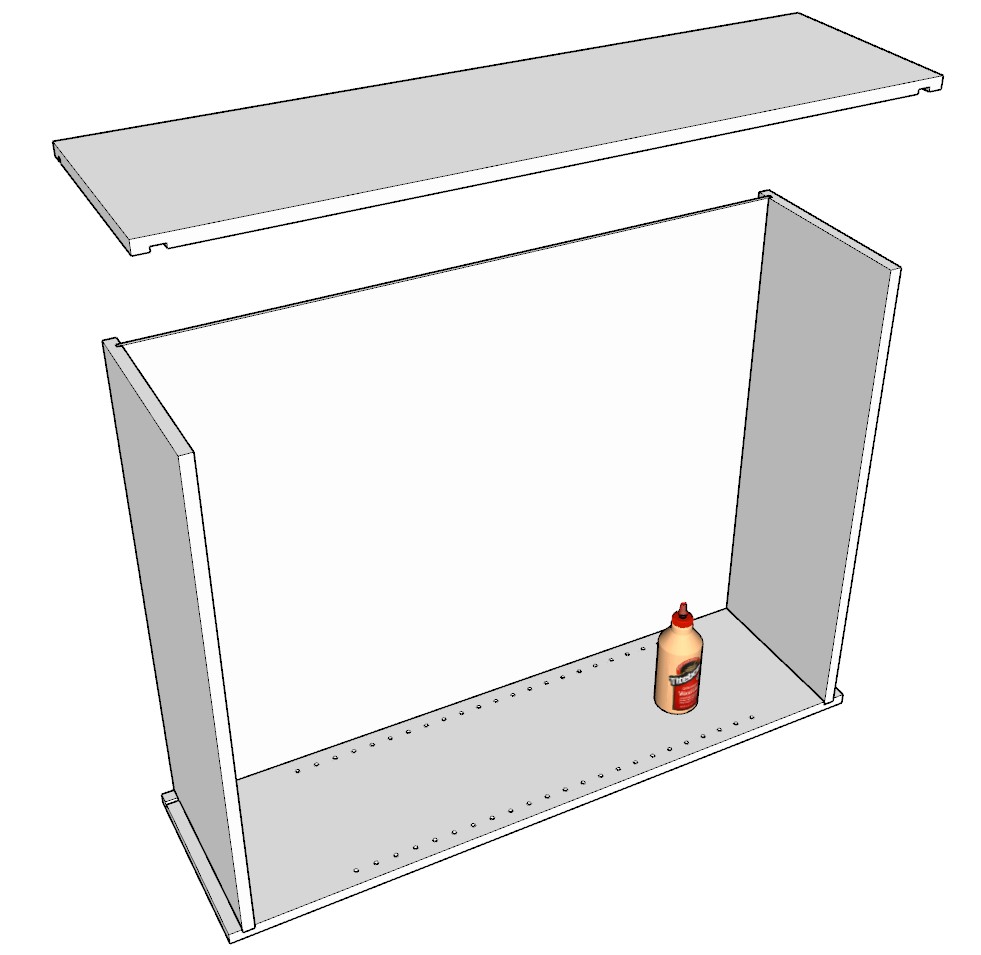
3.5 Clamp the Assembly
- Use wood clamps to hold the entire cabinet structure in place.
- Pro Tip: Tighten the clamps just enough to hold the structure securely. Do not overtighten, as it can squeeze out too much glue or warp the panels.
- Double-check the alignment to ensure all panels are square and flush before the glue sets.

3.6 Final Check
- Confirm that all components are properly aligned and flush at the edges.
- Clean up any excess glue with a damp cloth while it’s still wet.
- Leave the cabinet clamped and allow the glue to dry according to the manufacturer’s instructions (usually 24 hours).
Step 4: Add the Stretchers to the Cabinet Assembly
In this step, you will prepare and install two stretchers to reinforce the cabinet carcass and provide structural stability.
4.1 Gather Materials and Tools
- Materials:
- Two stretcher pieces: 30-1/2″ x 4-1/4″, cut from 3/4″ thick plywood
- Wood glue
- 1-1/4″ pocket screws
- Tools:
- Drill with pocket hole jig
- Clamps
- Pocket hole drill bit
4.2 Prepare the Stretchers
- Cut two stretcher pieces measuring 30-1/2″ x 4-1/4″ from the 3/4″ plywood.
- Set up a pocket hole jig and drill pocket holes along both ends of each stretcher as shown in the diagram.
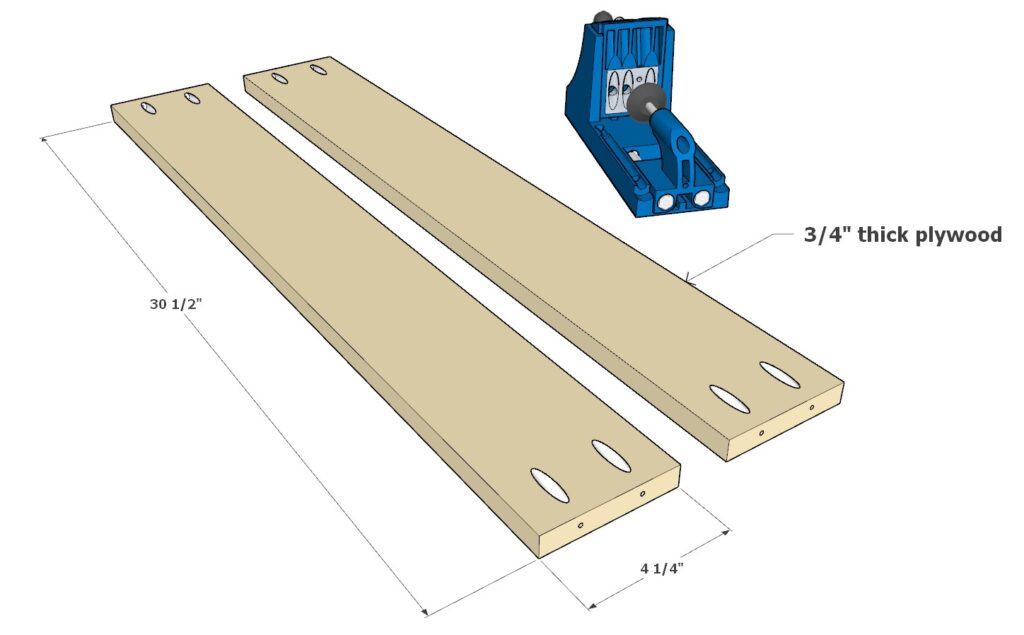
4.3 Attach the Stretchers
- Apply wood glue to the edges of the stretchers that will contact the cabinet carcass.
- Position the first stretcher across the top of the cabinet, making sure it aligns correctly with the carcass edges.
- Secure the first stretcher with 1-1/4″ pocket screws through the pre-drilled pocket holes.
- Repeat the process with the second stretcher at the lower part of the cabinet.

4.4 Check for Alignment
- Ensure the stretchers are flush with the edges of the cabinet carcass.
- Adjust with clamps as needed to maintain alignment while the glue sets.
- Wipe off any excess glue with a damp cloth.
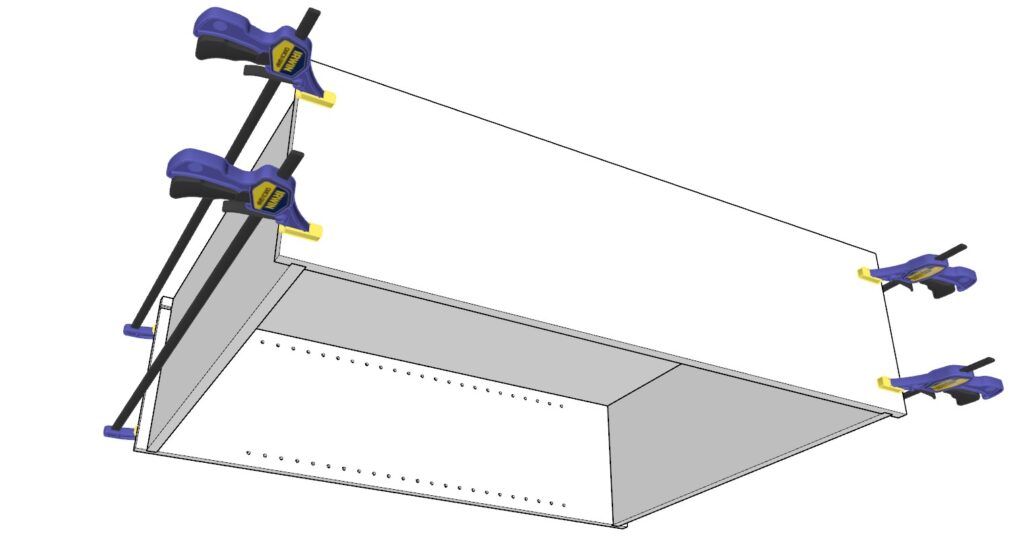
Step 5: Build and Attach the Face Frame
In this step, you will build the face frame to give your wall cabinet a polished and professional look, and attach it to the cabinet carcass. The face frame provides structural integrity and enhances the overall aesthetics.
5.1 Gather Materials and Tools
Materials:
- Two 1×2 lumber pieces, 28-15/16″ long
- Two 1×2 lumber pieces, 42″ long
- One 1×3 lumber piece, 39″ long
- Wood glue
- 1-1/4″ pocket screws
Tools:
- Pocket hole jig and drill
- Clamps
- Pin nailer with pin nails (optional)
- Sandpaper
5.2 Assemble the Face Frame
Cut the lumber pieces to size:
- Two 28-15/16″ pieces for the top and bottom rails
- Two 42″ 1×2 pieces for the vertical sides.
- One 39″ 1×3 piece for the center rail.
Set up your pocket hole jig and drill pocket holes at the ends of the horizontal pieces (as shown in the diagram).
- Tip: Ensure the pocket holes are positioned on the back side of the face frame to remain hidden after installation.
Apply wood glue to the ends of the vertical and horizontal pieces.
Assemble the frame by securing the pieces together with 1-1/4″ pocket screws. Use clamps to hold everything in place while driving in the screws.
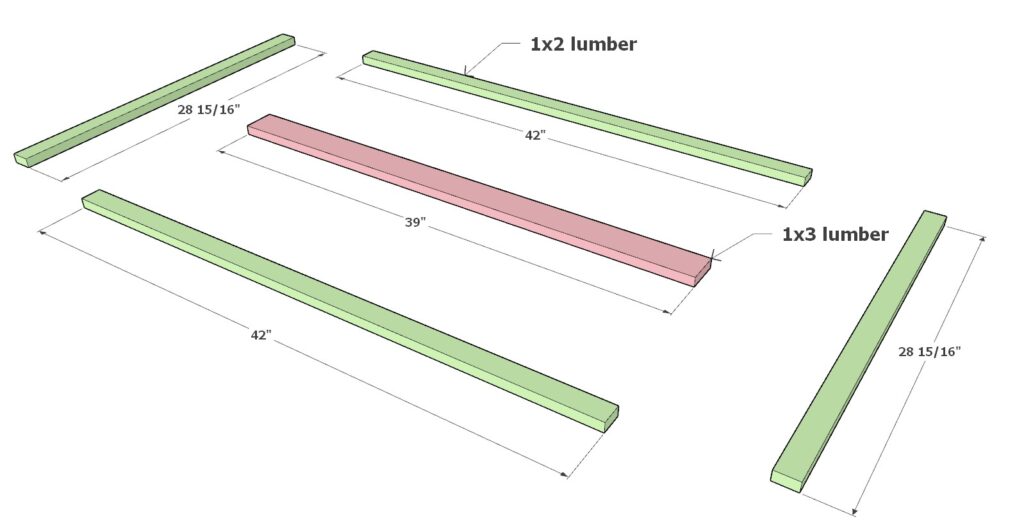
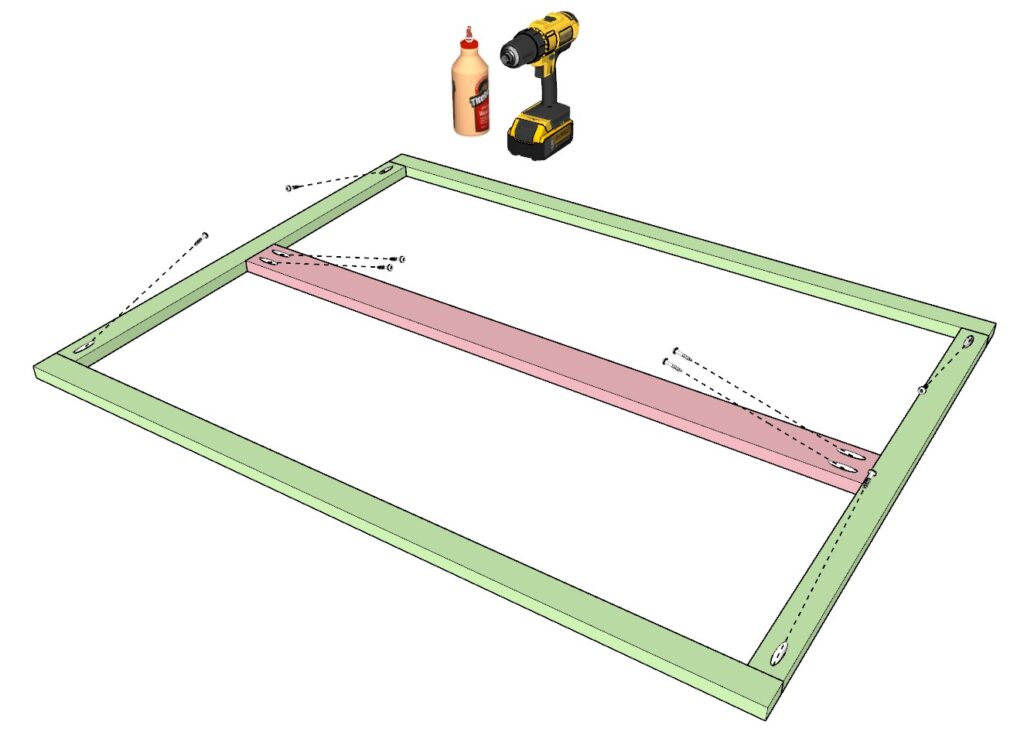
5.3 Prepare the Face Frame for Attachment
- Sand down the entire face frame to ensure smooth edges and eliminate any splinters.
- Tip: Pay extra attention to corners and joints to ensure they are flush and even.
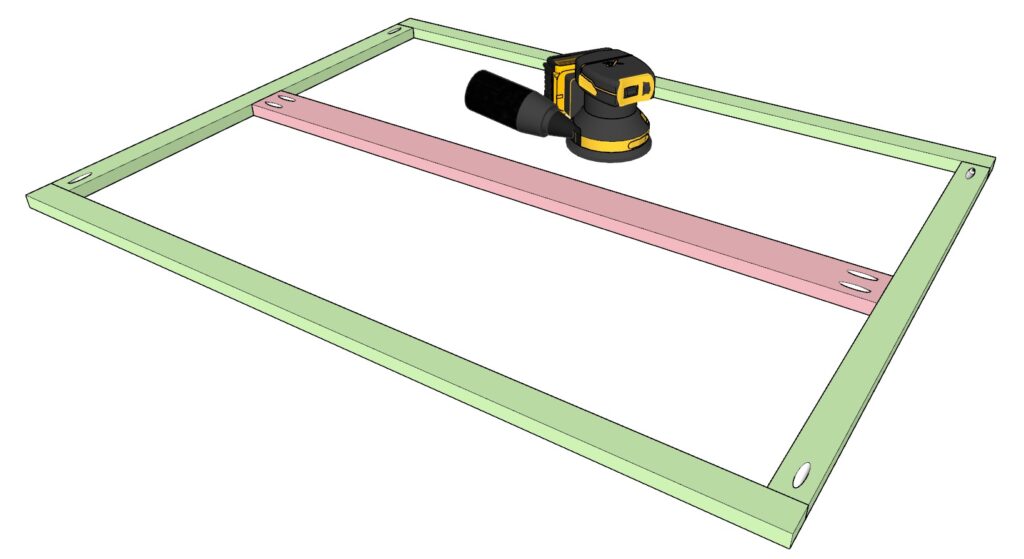
5.4 Attach the Face Frame to the Cabinet
Apply wood glue along the front edges of the cabinet carcass.
Position the face frame onto the cabinet carcass, ensuring it aligns perfectly with the edges of the cabinet.
If painting the cabinet:
- Use a pin nailer to drive pin nails directly through the face frame and into the cabinet carcass.
- Tip: The small holes from the pin nails can be easily filled and sanded smooth before painting.
If staining the cabinet:
- Avoid using pin nails to prevent visible holes. Instead:
- Use tape or clamps to hold the face frame securely in place while the glue dries.
- Avoid using pin nails to prevent visible holes. Instead:
Let the glue dry fully before moving on to the next steps.
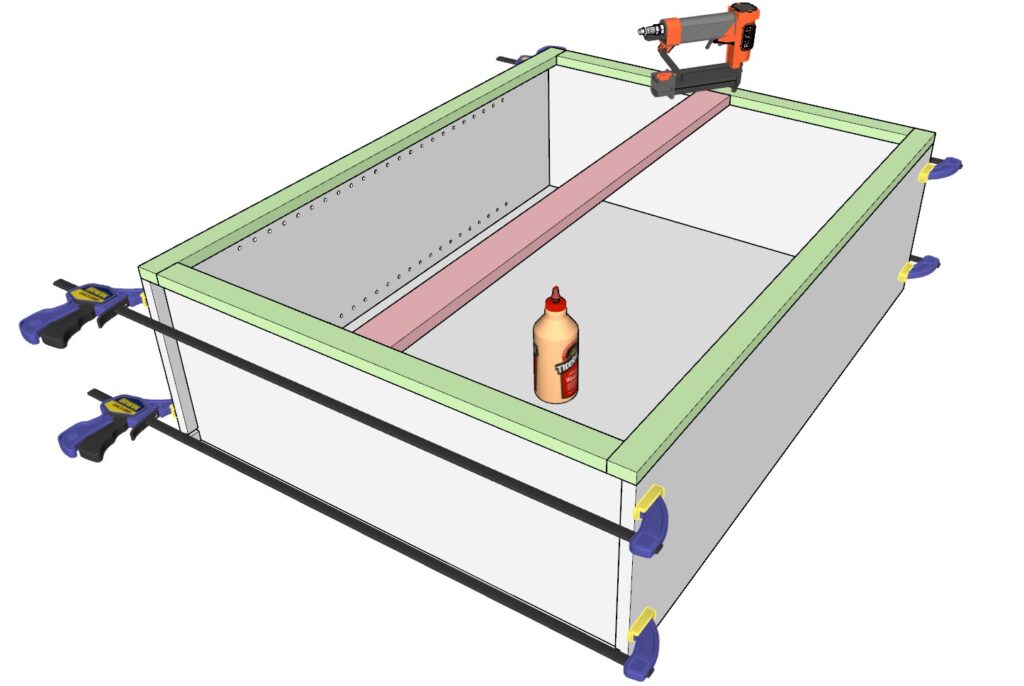
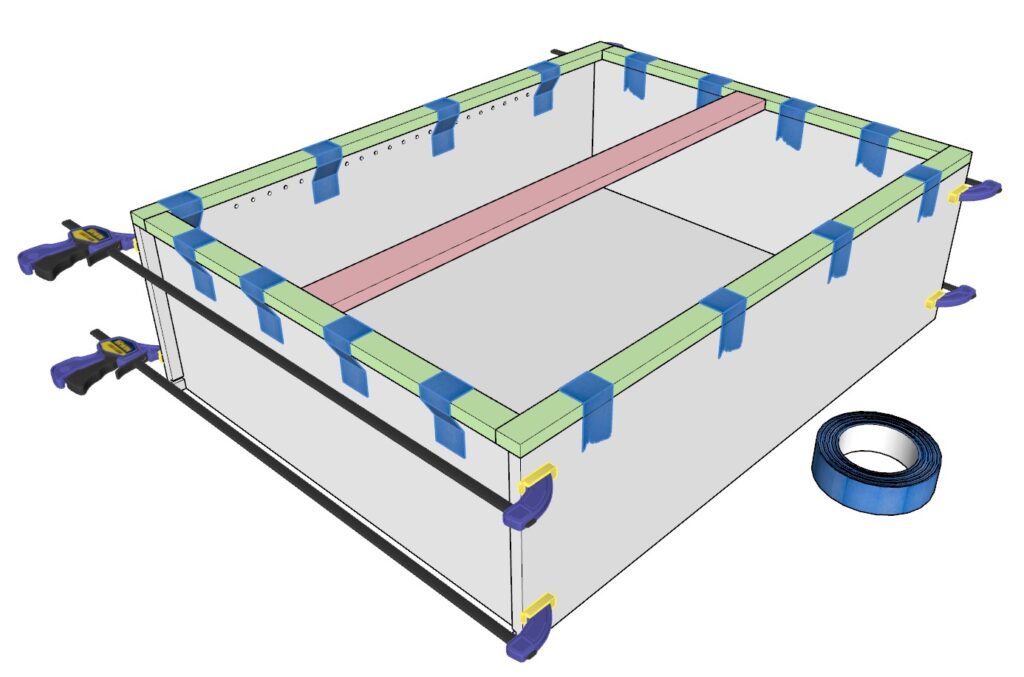
Step 6: Build and Install the Shelves
In this step, you’ll create two shelves and install them into the wall cabinet using shelf pins for adjustable placement.
6.1 Gather Materials and Tools
Materials:
- Two 30-1/2″ x 10-5/16″ (3/4″ thick plywood) pieces (for the shelf panels)
- Two 30-1/2″ 1×2 lumber pieces (for the shelf lips)
- Wood glue
- 1-1/4″ pocket screws
- Shelf pins (diameter matching the holes you drilled earlier)
Tools:
- Pocket hole jig and drill
- Clamps
- Sandpaper
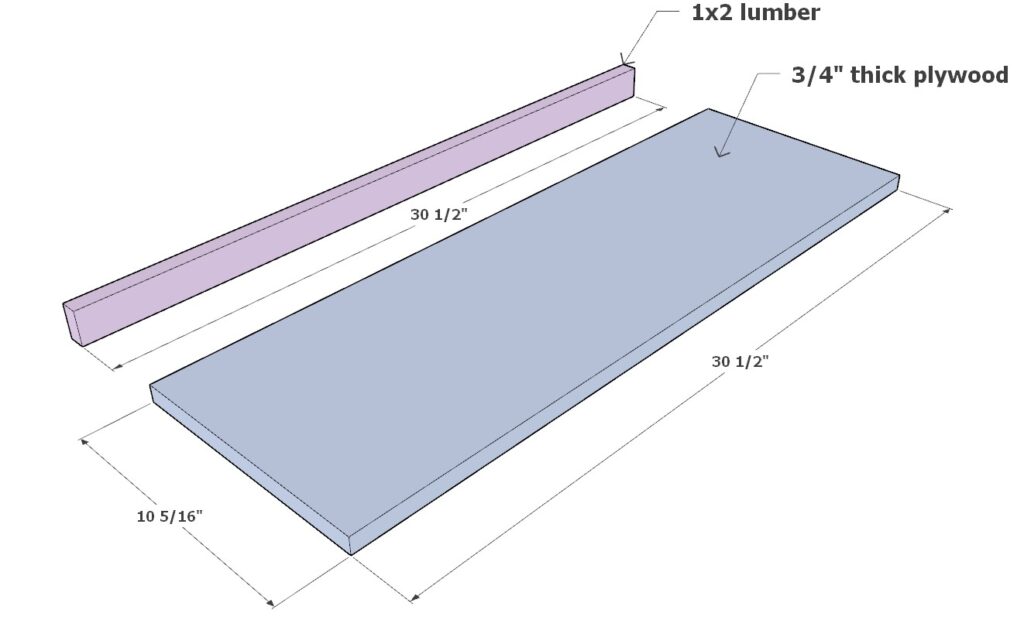
6.2 Build the Shelves
Prepare the shelf panels:
- Take a 30-1/2″ x 10-5/16″ plywood sheet. This will form the main body of the shelves.
Attach the shelf lip:
- Take the 1×2 lumber piece (30-1/2″ long) and align it flush with the front edges of the shelf panel.
- Apply wood glue along the edge of the plywood where the 1×2 lumber piece will sit.
- Pre-drill pocket holes on the underside of the plywood shelf panel to connect it to the 1×2 shelf lip securely.
- Use 1-1/4″ pocket screws to attach the 1×2 lumber piece to the plywood. Clamp the piece together to prevent shifting while screwing it in place.
Repeat this process to create two identical shelves.
- Tip: Sand the edges lightly to ensure smooth surfaces and prevent splinters.
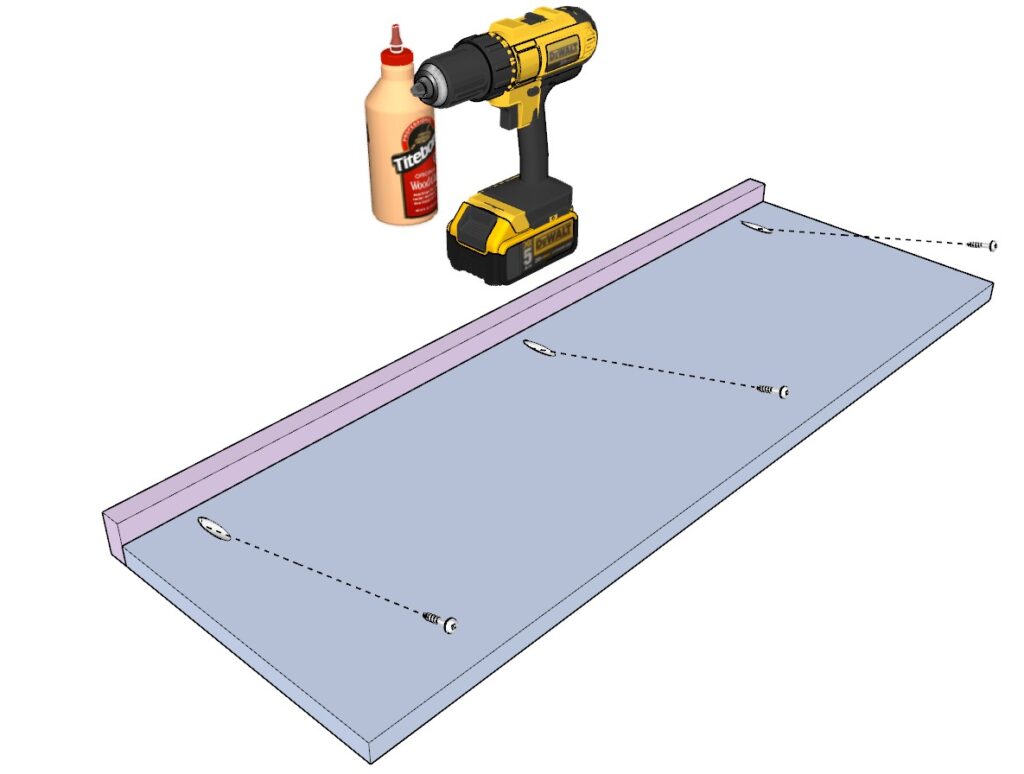
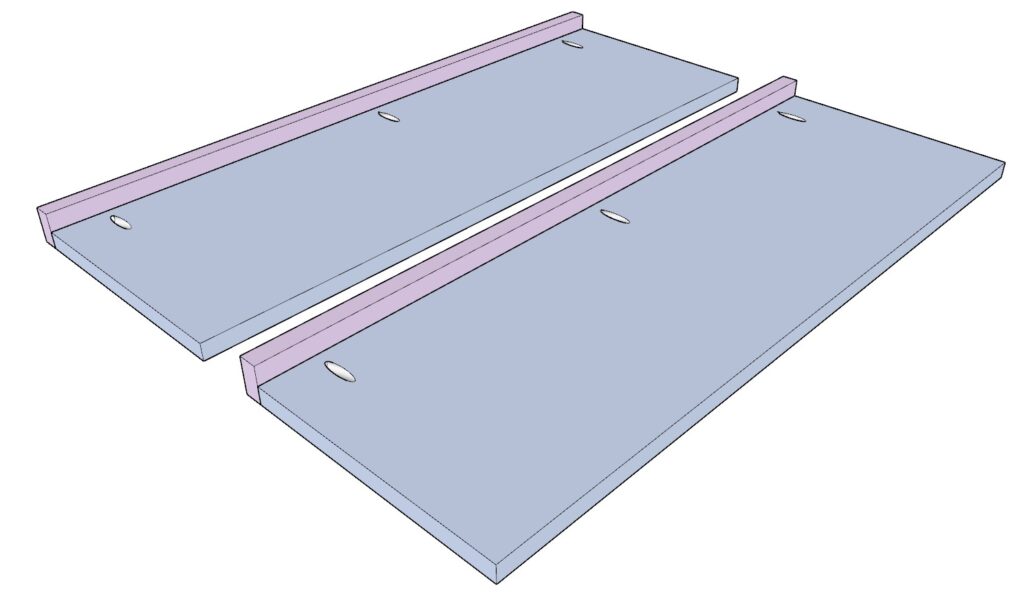
6.3 Install the Shelf Pins
Select the appropriate shelf pins:
- Use pins that match the diameter of the pinholes you drilled earlier (refer to Step 1 if needed).
- Common shelf pin diameters include 1/4″ or 5mm, but make sure your pins fit snugly into the pre-drilled holes.
Insert the shelf pins:
- Place the pins at the desired height in the side panels. Ensure all four pins are level to prevent the shelf from tilting.
6.4 Install the Shelves
- Carefully place the shelves onto the pins, ensuring that the shelf lips face forward for both shelves.
- Check for stability by pressing lightly on the shelves. Ensure the shelves sit evenly on the pins with no wobble.
- Tip: If there’s any looseness, adjust the shelf pins or sand the shelf edges lightly for a better fit.
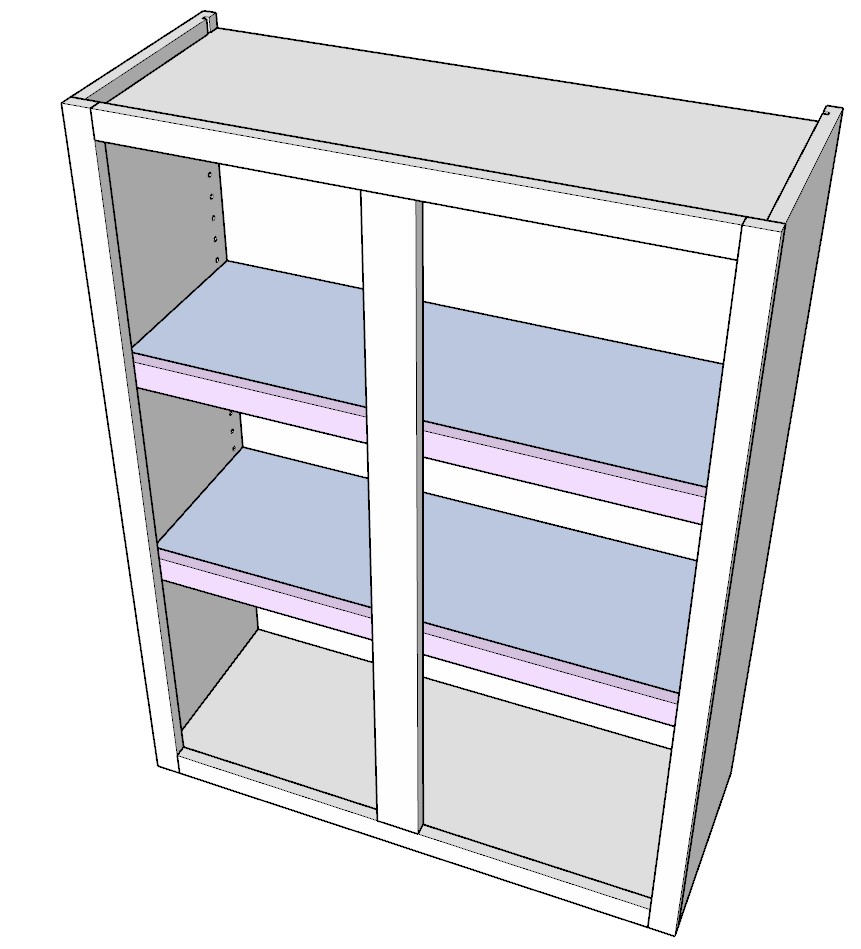
Step 7: Build and Assemble the Cabinet Doors
In this step, you’ll create two doors for the wall cabinet. Each door will feature 1×3 stiles and 1×2 rails, with a 1/4″ thick plywood panel in the center.
7.1 Gather Materials and Tools
Materials:
- 4 pieces of 1×3 lumber, 41-1/2″ long (door stiles – vertical pieces)
- 4 pieces of 1×2 lumber, 9-3/4″ long (door rails – horizontal pieces)
- 2 pieces of 1/4″ thick plywood (38-7/8″ long x 10-1/4″ wide)
- Wood glue
Tools:
- 3/4″ tongue and groove router bit set
- Clamps
- Sandpaper
7.2 Prepare the Stiles and Rails
Cut grooves in the stiles:
- Use the groove router bit from your 3/4″ tongue and groove router bit set.
- Cut a 1/4″ wide x 1/4″ deep groove along the center of both 41-1/2″ long 1×3 stiles.
- These grooves will hold the plywood panel securely in place.
Prepare the rails:
- Using the same groove router bit, cut a 1/4″ wide x 1/4″ deep groove along the center of both 9-3/4″ long 1×2 rails.
- Switch to the tongue bit and cut a tongue on both ends of each rail. The tongue will fit into the grooves of the stiles during assembly.
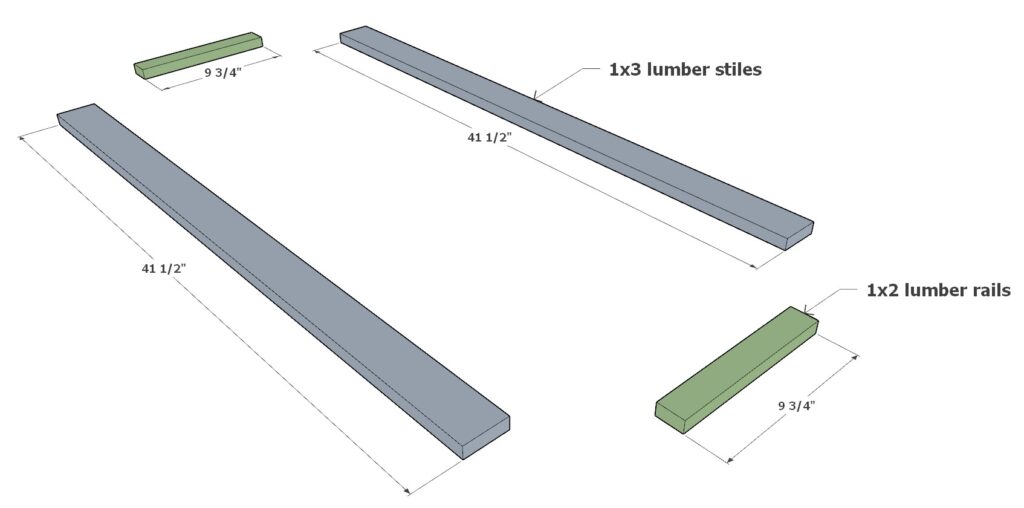
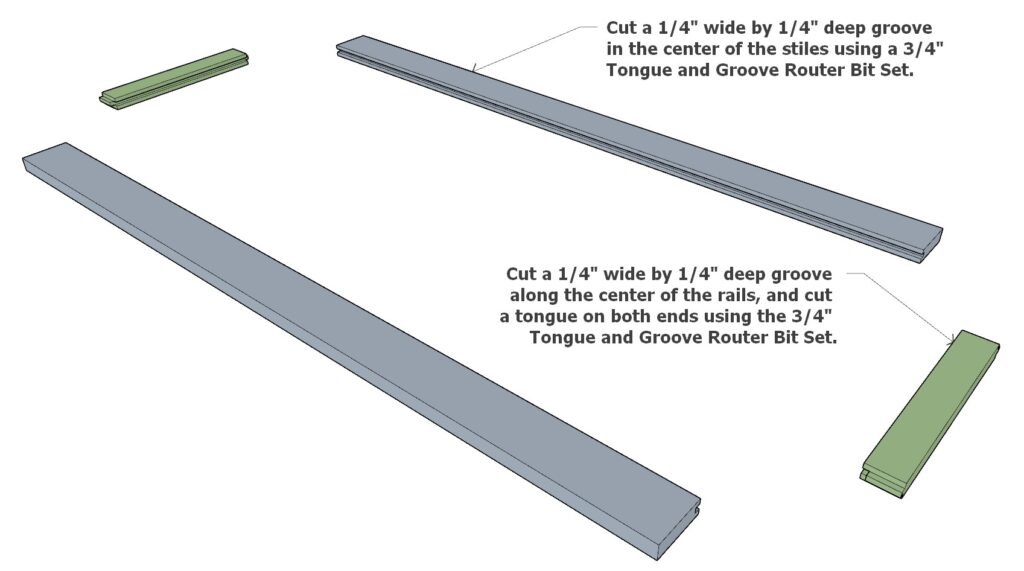
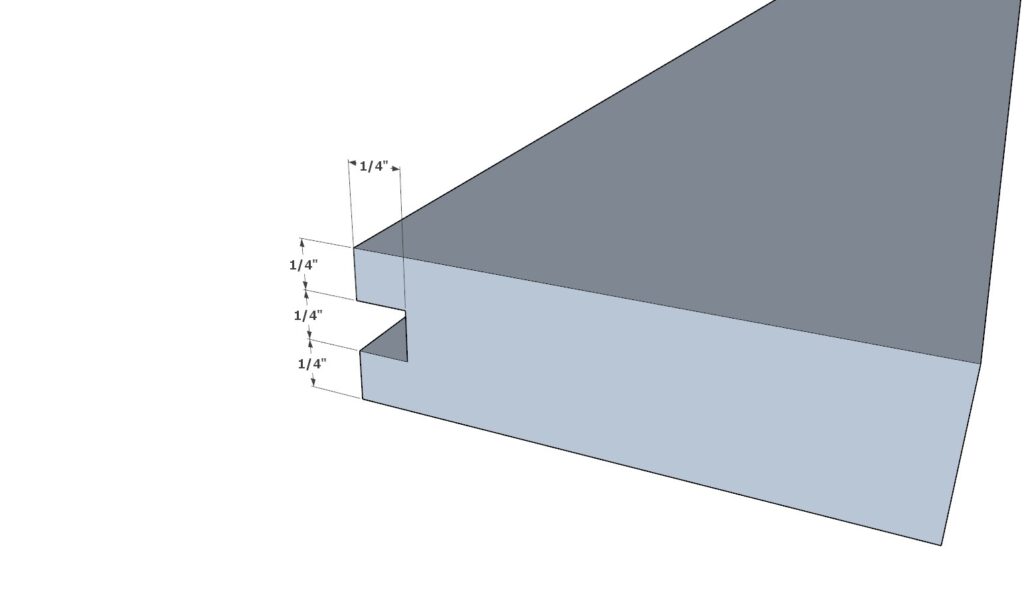
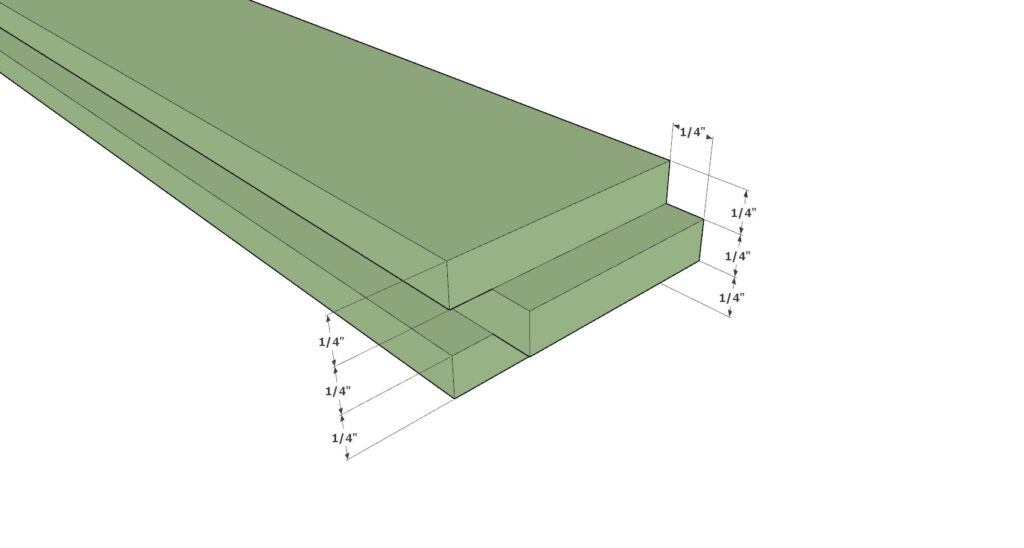
7.3 Assemble the Door Panels
Insert the plywood center panel:
- Slide the 1/4″ plywood panel (38-7/8″ long x 10-1/4″ wide) into the grooves of one stile and position it so that it fits snugly.
- Make sure the plywood fits into the groove with no gaps or overhangs. If needed, sand the edges slightly for a perfect fit.
Attach the rails:
- Apply wood glue to the tongues of the rails and fit them into the grooves of the stile that already holds the plywood panel.
- Repeat the process for the second stile, sliding it onto the opposite side of the panel and securing it to the rails with wood glue.
Clamp the door frame:
- Use wood clamps to hold the entire door frame together while the glue dries.
- Ensure that the frame is square by measuring the diagonals. If the diagonals are equal, the door is square. If not, adjust the clamps slightly.
Allow the glue to dry fully (follow the glue manufacturer’s recommendations for drying time).
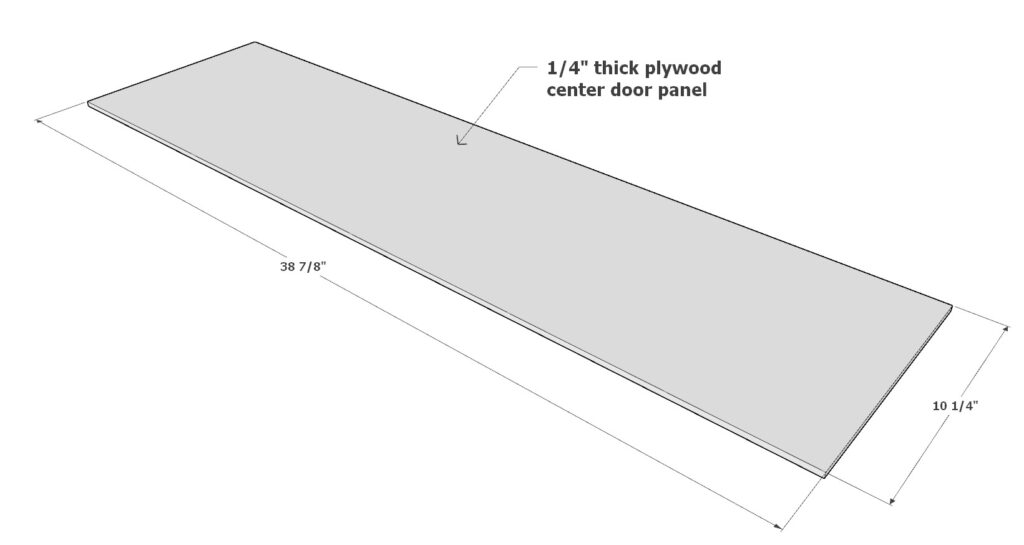
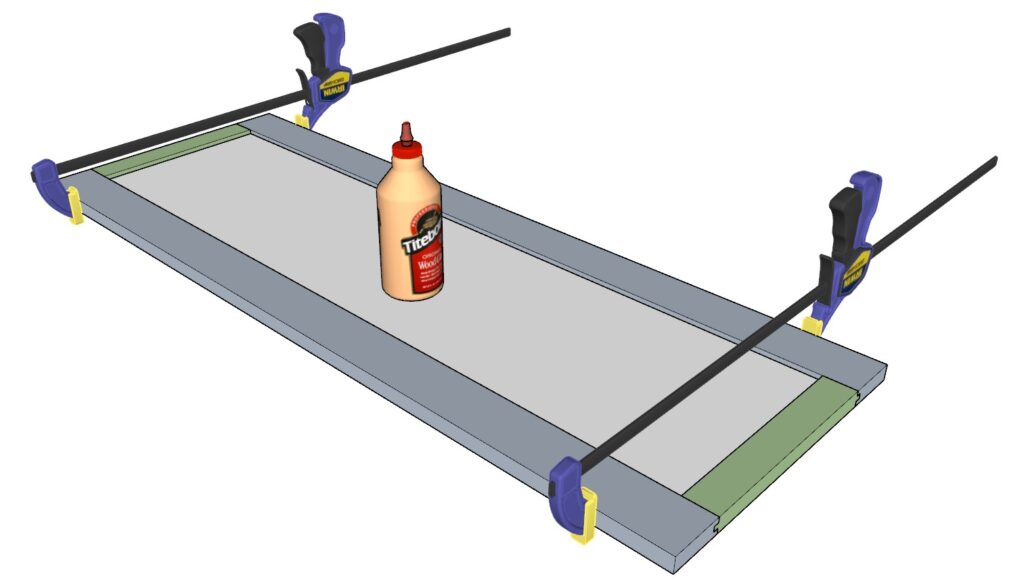
7.4 Make the Second Door
- Repeat the process to create the second identical door.
- Follow the same steps as above to cut the stiles and rails, assemble the frame, and insert the plywood panel.
7.5 Sand and Prepare the Doors for Installation
Sand the doors:
- Use fine-grit sandpaper to smooth all surfaces, paying attention to any glue squeeze-out or rough edges.
- Make sure the doors are clean and smooth, ready for painting or staining.
Prepare for installation:
- Verify that the doors are square and that their dimensions match the cabinet opening. If needed, trim the edges slightly to ensure a perfect fit.
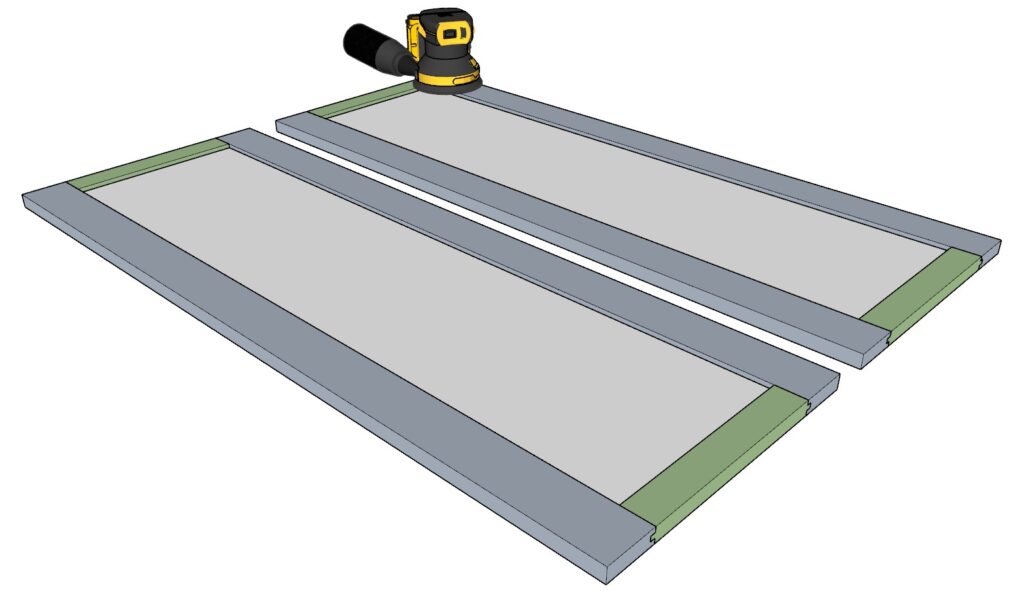
Step 8: Attaching Euro Hinges
In this step, you’ll install the soft-close cabinet door hinges. We’ll be using the Kreg KHI-HINGE Concealed Hinge Jig to ensure precise and easy hinge installation.
To see a visual example of how to attach hinges, refer to this YouTube video.
Tools and Materials Needed:
- Soft-Close Hinges: 1/2″ partial overlay with a 100-degree opening angle.
- Kreg KHI-HINGE Concealed Hinge Jig: For accurate hinge cup hole placement.
- 35mm Forstner Bit: Included with the Kreg jig.
- Power Drill: For drilling hinge cup holes and pilot holes.
- Clamps: To hold the jig and door securely.
- Pencil and Measuring Tape: For marking hinge positions.
- Screws: Provided with the hinges for securing the hinges and mounting plates.
Step 8.1: Prepare and Mark Hinge Locations
- Mark Hinge Locations on the Door: Measure 4 inches from the top and bottom edges of each cabinet door and mark these spots. This spacing is standard for most cabinet doors, offering balanced support and functionality.
- Position the Kreg Jig: Place the Kreg hinge jig at the marked spots on the door. Ensure the jig is correctly set for the desired cup distance (commonly 3mm from the door edge), aligning the index line on the jig with the marks.
Step 8.2: Drill the Hinge Cup Holes
- Set Up the Kreg Jig: Adjust the jig’s settings for the proper cup distance and depth. Most concealed hinges require a 12-13mm (about 1/2 inch) depth for the hinge cup.
- Drill the Holes: Using the 35mm Forstner bit, drill the cup holes at the marked spots. The Kreg jig’s stop collar will prevent you from drilling too deep, ensuring the hole is at the correct depth for the hinge to sit flush with the door surface.
Step 8.3: Attach Hinges to the Door
- Insert the Hinges: Fit the hinges into the drilled cup holes, ensuring they sit flush and aligned.
- Secure the Hinges: Use the provided screws to attach the hinges securely to the door. Avoid overtightening to prevent damage to the door or stripping the screws.
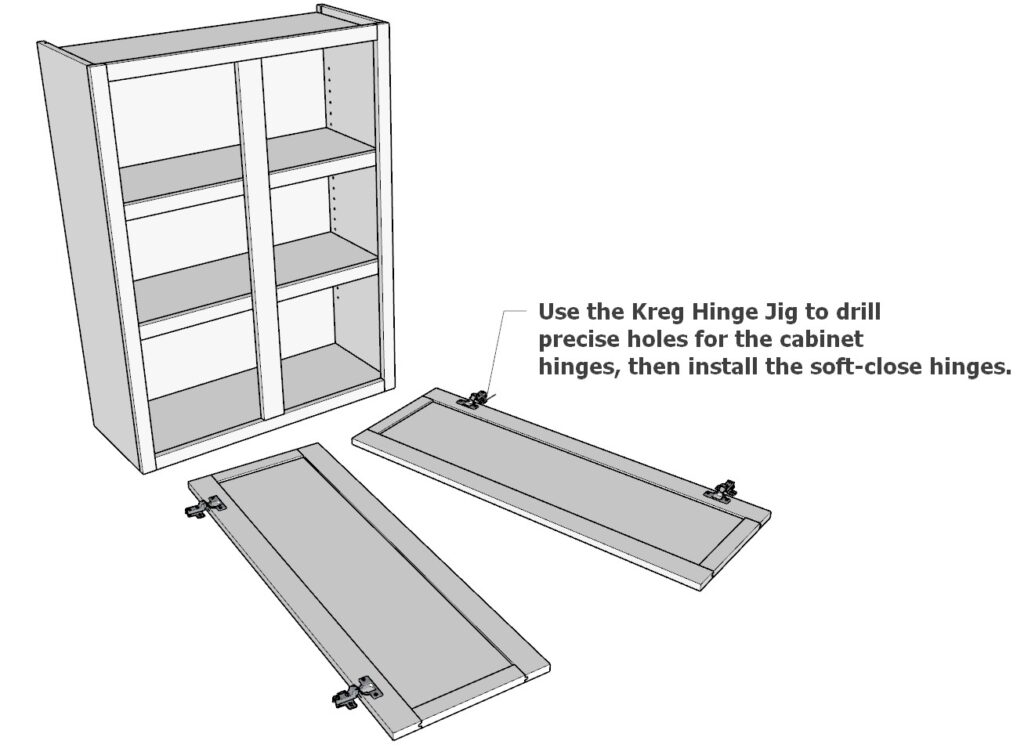
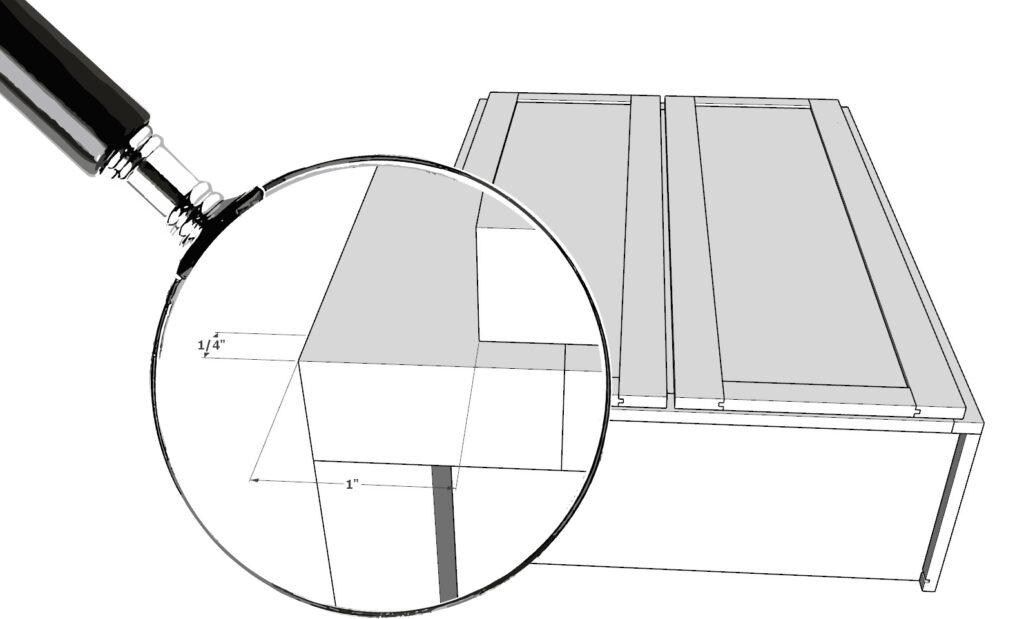
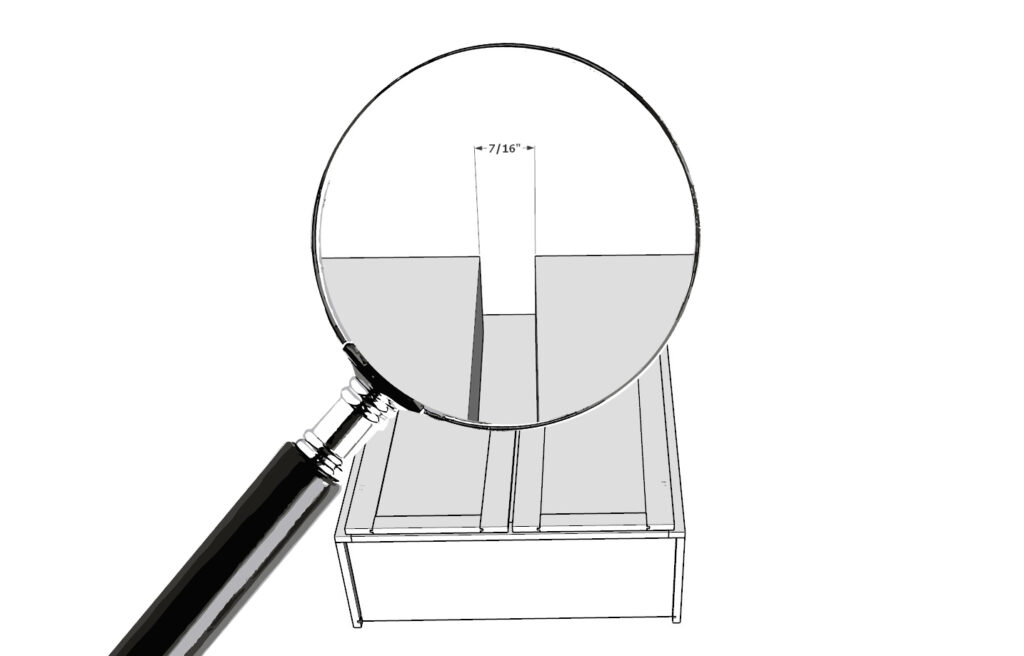

Final Step: Preparing and Painting Your Cabinets
Achieving a smooth, professional finish on your cabinets requires careful preparation and precise painting techniques. This step combines the preparation and painting processes into one comprehensive guide.
Step 1: Preparing the Cabinets for Painting
Clean the Cabinets:
- Start by thoroughly cleaning all cabinet surfaces with a degreaser like Trisodium Phosphate (TSP) or a commercial degreasing product. This step is crucial to remove grease, dirt, and other residues that can affect paint adhesion.
Sanding:
- Sand all surfaces with 120- to 150-grit sandpaper to create a rough texture for the primer to adhere to. Use a random orbital sander for flat surfaces and sanding sponges for detailed areas.
- After the initial sanding, progress to finer grits, such as 180-220, to smooth the surfaces while maintaining enough texture for the primer.
Fill Imperfections:
- Fill any gaps, holes, or imperfections with a high-quality wood filler. Sand these areas smooth once the filler is dry.
Remove Dust:
- Use a vacuum with a brush attachment, followed by a tack cloth, to remove all sanding dust from the surfaces. This ensures a clean base for the primer.
Step 2: Priming the Cabinets
- Apply Primer:
- Use a high-quality bonding primer suitable for cabinetry. Apply a thin, even coat using a brush, roller, or spray gun. Make sure to cover all surfaces, including edges and detailed areas.
- Let the primer dry according to the manufacturer’s instructions, then lightly sand with 220-grit sandpaper to remove any rough spots. Wipe down with a tack cloth to remove dust.
Step 3: Painting the Cabinets
Option A: Using a Spray Gun
Set Up the Spray Gun:
- Use an HVLP (High Volume Low Pressure) spray gun or an airless sprayer with a fine finish tip. Adjust the spray gun settings based on the paint’s viscosity and the manufacturer’s recommendations.
Test the Spray Pattern:
- Practice spraying on a piece of cardboard or scrap material to ensure an even spray pattern without runs or spitting.
Spray the Paint:
- Begin by spraying edges and detailed areas first, then move to flat surfaces. Hold the gun perpendicular to the surface and maintain a consistent distance of about 6-8 inches.
- Use a 50% overlap on each pass to ensure uniform coverage. Move the gun at a steady pace to avoid uneven paint application.
Apply Multiple Coats:
- Apply multiple thin coats, allowing each to dry fully and lightly sanding between coats with 320- to 400-grit sandpaper. This helps achieve a smooth, factory-like finish.
Option B: Using a Brush and Roller
Brush Edges and Details:
- Use a high-quality synthetic brush for edges and detailed areas. Apply the paint in long, smooth strokes to minimize brush marks.
Roll Larger Surfaces:
- For larger, flat areas, use a mini foam roller designed for smooth surfaces. Roll in one direction with light pressure to achieve an even coat.
Sand Between Coats:
- Lightly sand between coats with fine-grit sandpaper (320-400 grit) and wipe with a tack cloth. This step is essential to maintain a smooth finish.
Apply Final Coat:
- Apply the final coat slightly wetter to achieve a smooth, glass-like appearance. Allow for extended drying time on the final coat to ensure a durable, long-lasting finish.
Final Touches:
Inspect and Touch Up:
- Check all surfaces under bright light for imperfections. Touch up any areas with a fine brush.
Reassemble the Cabinets:
- Once fully cured, reattach all hardware and rehang doors and drawers. Adjust as needed to ensure everything aligns properly.
Curing Time:
- Allow the paint to cure completely before heavy use. Curing times vary, but a few days to a week is typically recommended for full hardness and durability.
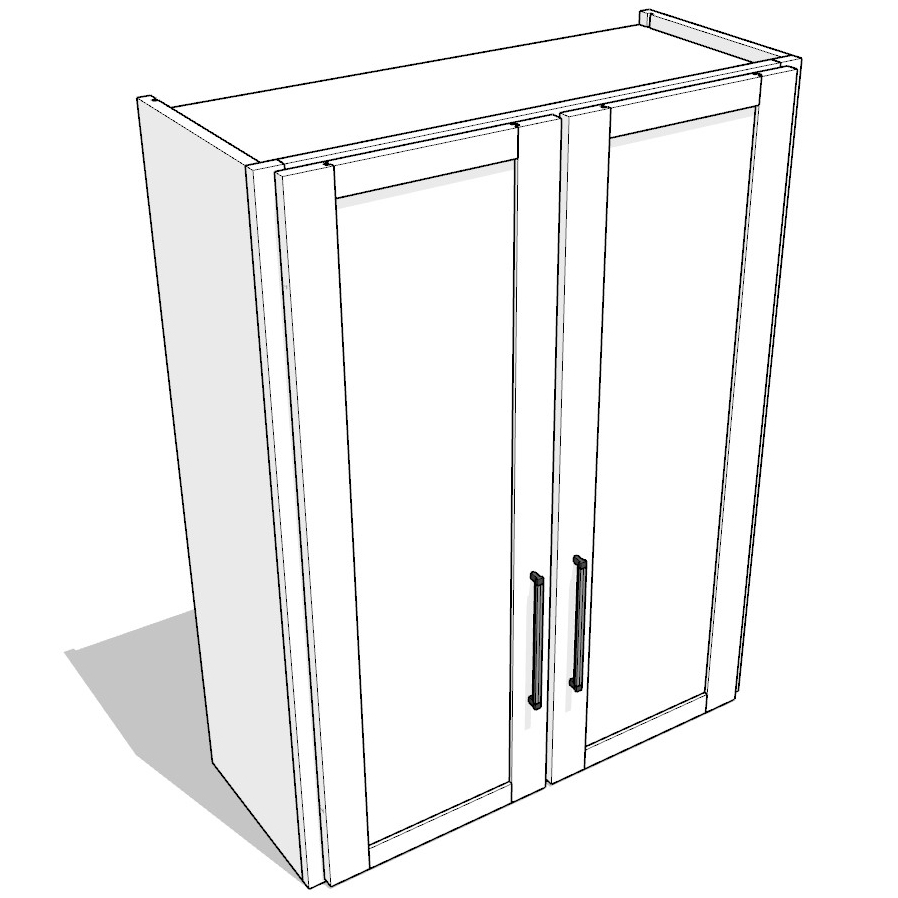